Диоксид титана TiO2 полиморфен, он кристаллизуется в двух сингониях: брукит — в ромбической, рутил и анатаз — в тетрагональной, но последние различаются строением кристаллической решетки. В обоих случаях каждый атом титана находится в центре октаэдра и окружен 6 атомами кислорода. Пространственное же расположение октаэдров разное: в анатазе на каждый октаэдр приходится 4 общих ребра, в рутиле только 2. Элементарная ячейка анатаза состоит из четырех молекул, а рутила только из двух:

Благодаря более плотной упаковке ионов в кристаллах рутил превосходит анатаз по стабильности, плотности, твердости, показателю преломления, диэлектрической постоянной и обладает пониженной фотохимической активностью. При температуре 915 0C ‑ 950 0C анатаз переходит в рутил, но полученный при этом рутил отличается высокой абразивностью и низкой дисперсностью. В 1949 г. была найдена возможность управления кристаллизацией введением рутилизирующих добавок и зародышей. Ионы Zn2+, Mg2+, Al3+, Sn2 + являются стабилизаторами рутильной формы, ионы SO42-, PO43 - — анатазной. В присутствии даже малых количеств соединений фосфора переход анатаза в рутил становится невозможным. Рутилизирующие зародыши получают, обрабатывая гидратированный диоксид титана после пятой стадии промывки раствором едкого натра. При этом образуется тетратитанат натрия Na2Ti4O3, который обрабатывают соляной кислотой, и пептизируют продукт гидролиза, предварительно освобожденный от ионов SO42-. Такие зародыши вводятся перед прокаливанием.
Рутил, прокаленный при температуре около 10000C и содержащий примеси Fe, Cr, Ni, Mn, проявляет свойство фототропии. При освещении он становится коричневым, в темноте вновь светлеет. Это объясняется окислением примесных металлов в высшие оксиды вследствие выделения кислорода при освещении ТiO2 с деформированной решеткой.
В чистом виде диоксид титана, особенно в анатазной форме, обладает высокой фотохимической активностью, что вызывает разрушение лакокрасочной пленки («меление») и выцветание органических пигментов. Модифицирование поверхности частиц диоксида титана гидроксидами Al, Si, Zn резко уменьшает фотохимическую активность.
Диоксид титана химически инертен, нерастворим в слабых кислотах и щелочах и органических растворителях. Не ядовит, ПДК в воздухе рабочих зон 10 мг/м3. Может применяться со всеми видами пленкообразователей и растворителей. Пригоден для водоэмульсионных, воднодисперсионных и порошковых красок. Пигментный диоксид титана также широко используется для окрашивания изделий из резины, пластмасс, линолеума, бумаги и химических волокон. Кроме пигментного диоксида титана, содержащего 82—95 % (масс.) TiO2, вырабатывается диоксид титана для твердых сплавов, стекол, керамики с более высоким содержанием TiO2.
Сырье, для получения диоксида титана. Для переработки в пигментный диоксид титана используются минералы: природный рутил, содержащий 92—95 % (масс.) TiO2 и примесь Fe2O3, придающую ему красный цвет (рутил красный); ильменит FеО*ТiO2 или — арканзитFe2O3*3ТiO2; титаномагнетиты,
состоящие из зерен ильменита и магнетита и содержащие 8—12 % (масс.) TiO2.
В чистом виде титансодержащие минералы встречаются редко. Для освобождения от примесей других минералов и пустой породы измельченные руды подвергают магнитному и другим видам обогащения и получают концентраты примерного состава, % (масс.):
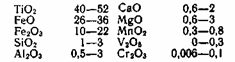
Технология производства пигментного диоксида титана. Переработка титановых концентратов и шлаков в пигментный диоксид титана имеет целью не только освобождение от примесей, но и придание TiO2 требуемой кристаллической формы, дисперсности, адсорбционных свойств и подавление фотохимической активности. Для получения диоксида титана применяют два способа: сернокислотный — для концентратов, содержащих более 40 % TiO2, и хлоридный,— экономически выгодный только для переработки концентратов, содержащих не менее 80 % TiO2 (так как получаемые отходы FeCl3 не находят применения).
Сернокислотный способ. Это тонкий и сложный процесс, состоящий из трех основных стадий и ряда вспомогательных операций (см. схему 2.1).
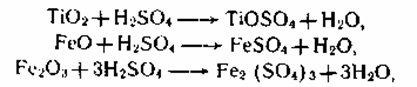
1. Первой стадией является разложение тонкоизмельченного
титан-содержащего
концентрата 85—92 %-ной серной кислотой при 180—220 0C и непрерывном перемешивании реакционной массы сжатым воздухом с получением прозрачного раствора титанилсульфата TiOSO4. При этом протекают следующие экзотермические реакции разложения:
а также аналогичные реакции с оксидами Mn, Ca, Al и другими примесями. Все реакции протекают бурно после предварительного нагрева с выделением большого количества паров воды, H2SO4, SO3 и SO2, которые улавливаются в скруббере, орошаемом водой. Реакцию разложения проводят периодическим методом.
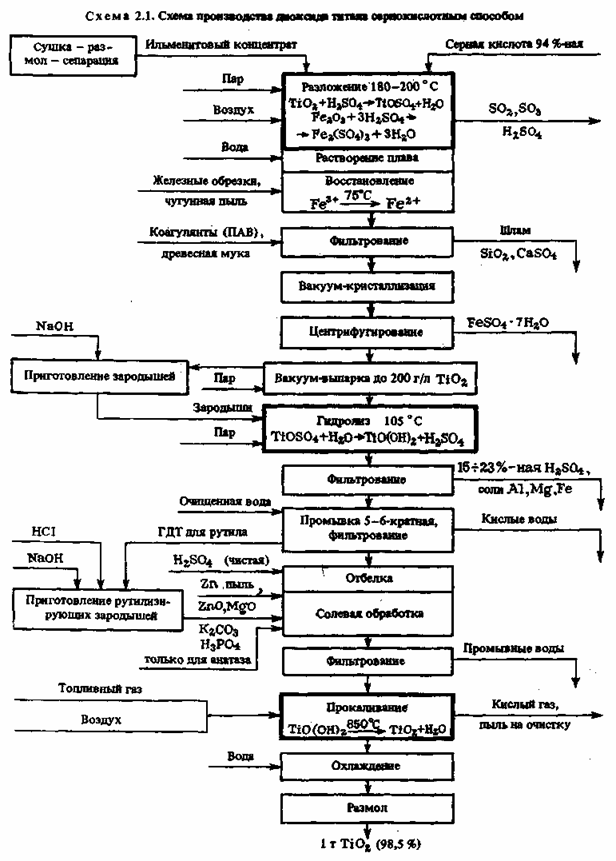
Многочисленные попытки применения реакторов непрерывного действия с механическим перемешиванием не оправдали себя как технически, так и экономически, так как наблюдался большой коррозионный и эрозионный износ аппаратуры.
Кислые растворы сульфатов титана, железа и других элементов, присутствующих в сырье, имеют сложный коллоидно-химический состав, изменяющийся в зависимости от содержания кислоты, температуры, времени выдержки.
При проведении реакции разложения реактор непрерывно продувают сжатым воздухом, который перемешивает суспензию, а затем при кристаллизации солей и застывании плава делает его пористым. После окончания реакции разложения и охлаждения плава выход по титану составляет 96—98 %. В реактор подают воду (из расчета получения раствора с содержанием TiО2 примерно 120 г/л) и все водорастворимые соли переходят в раствор.
Для последующего удаления сульфата железа(II) из раствора титанилсульфата проводят восстановление ионов Fe3+ до Fe+, для чего в реактор добавляют чугунную стружку. В кислой среде проходит реакция восстановления Fe3+ ——>- Fe2+ выделяющимся водородом. Одновременно восстанавливается и небольшое количество (3—5 г/л) Ti4+ до Ti3+. Соединения Ti3+ являются сильными восстановителями, они исключают возможность повторного окисления воздухом Fe2+ и этим предотвращают адсорбцию ионов Fe3+ на диоксиде титана, придающих ему желтую окраску.
Кислые растворы титанилсульфата, сульфатов железа, алюминия, марганца отстаивают или отфильтровывают от шлама, состоящего из остатков неразложившейся руды, диоксида кремния, нерастворимого сульфата кальция, а затем осветляют, отделяя коллоидные частицы коагуляцией с помощью флокулянтов — высокомолекулярных ПАВ. После вакуум-кристаллизации железный купорос FeSO4*7H2O отделяют от раствора центрифугированием или фильтрованием. Железный купорос является побочным продуктом производства.
2. Важнейшей стадией, определяющей пигментные свойства диоксида титана, является термический гидролиз титанилсульфата, протекающий по реакции:

Это уравнение не раскрывает сложного хода реакции гидролиза и полного состава получаемых веществ. Титанил-ионы в водном растворе образуют гидроксокомплексы I, II, в которых атомы титана связаны через оловые мостики. При термическом гидролизе происходит переход оловых мостиков в оксо-связи:
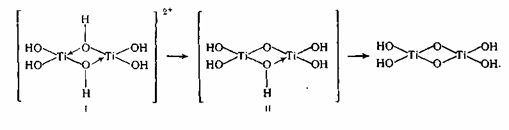
Такой продукт гидролиза по брутто-составу примерно соответствует TiO(OH)2 и его называют метатитановой кислотой
(MTK). Фактически часть основных групп в полиионе замещены на сульфогруппы, которые частично сохраняются в виде концевых групп и в продукте гидролиза, имеющем полимерное строение и называемом гидратированным диоксидом титана (ГДТ): TiO2*0,71H2O*0,07SO3.
Для ускорения гидролиза и повышения выхода, а главное, для получения частиц ГДТ определенного размера в предгидролизный раствор вводят специально подготовленные зародыши. Для получения зародышей отбирают 0,3—0,5 % (масс.), в расчете на TiO2, предгидролизного кислого раствора в отдельный реактор, где при непрерывном перемешивании его нейтрализуют раствором NaOH до рН = 3. При этом выпадает коллоидный осадок гидрозоля гидроксида титана, после 1—2-часовой выдержки при 60—80 0C переходящий в микрокристаллические зародыши переменного состава. Условия приготовления зародышей определяющее влияют на процесс гидролиза и качество пигмента.
Так как в растворах с концентрацией TiO2 < 200 г/л рано наступает коагуляция продуктов гидролиза, что препятствует кристаллохимическому росту частиц, предгидролизные растворы предварительно концентрируют до содержания в них TiO2 200—240 г/л. Это осуществляют в вакуум-выпарных аппаратах при 60 0C. Гидролиз проводят в реакторах, снабженных мешалкой и змеевиками для обогрева и охлаждения. Подготовленный предгидролизный раствор нагревают, вводят зародыши, доводят до кипения (105—1100C), разбавляют водой и продолжают кипятить до 96—97 %-ного превращения титанилсульфата в ГДТ, который отделяют от раствора фильтрованием и промывают водой. Сульфаты [FeSO4, MnSO4, А12(SО4)3] в кислой среде не гидролизуются и остаются в растворе серной кислоты.
Осажденный ГДТ подвергают 3—6-кратной промывке, на последних стадиях деминерализованной водой. Однако полностью отмыть прочно адсорбированные ионы Fe3+ не удается. Для удаления оставшихся ионов Fe3+ проводят «отбелку»: ионы Fe3+ восстанавливают водородом до Fe2+, для чего вводят порошок металлического цинка и химически чистую серную кислоту. После отбелки проводят солевую обработку, добавляя для получения рутильной формы TiO2 до 3 % (масс.) ZnO и специально приготовленные рутилизирующие зародыши. Для получения анатазной формы TiO2 вводят минерализатор К2СО3, облегчающий удаление воды при прокаливании, и 0,5 % фосфорной кислоты, стабилизирующей анатазную форму.
3. Следующей стадией является
прокаливание ГДТ с получением диоксида титана:

При прокаливании вместе с водой удаляется и SO3 [состав ГДТ TiO2*0,71H2O*0,07SO3].
Прокаливание проводят в трубчатых вращающихся печах при температуре 850—900 0C, время пребывания продукта в печах — около 8 ч. Выходящие из печей дымовые газы подвергаются мокрой очистке от SO3, Н2SO4 и уносимой газами пыли ТiO2 в скрубберах, орошаемых аммиачной водой. Полученный диоксид титана охлаждают и размалывают.
4. Заключительными операциями получения пигментного диоксида титана являются мокрый размол, классификация частиц по размерам и поверхностная обработка (см. схему). Предварительно измельченный в сухом виде диоксид титана репульпируют в очищенной воде (300— 350 г/л TiO2), добавляют силикат натрия и щелочь и подвергают
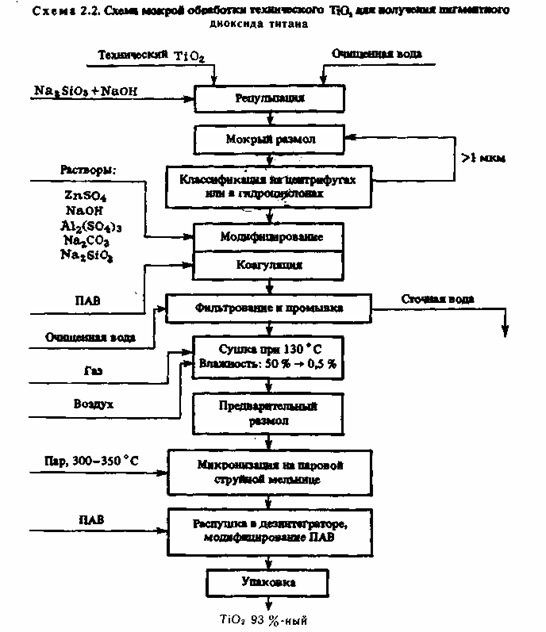
непрерывному мокрому размолу в шаровой или в бисерной мельнице. Вытекающая из мельницы пульпа направляется для классификации частиц в гидроциклоны или центрифуги. Отделенные частицы размерами более 1 мкм возвращают на повторный размол.
Пульпу с частицами менее 1 мкм подвергают солевой обработке растворами Al(SO4)3, NaOH, Na2SiO3, ZnSO4и коагулируют. Осадок TiO2 отфильтровывают и отмывают от ионов Na + и SO42-. В зависимости от дальнейшего назначения диоксид титана обрабатывают модификаторами — ПАВ или кремнийорганическими соединениями. Полученный пигментный диоксид титана сушат, подвергают микронизации и упаковывают. На предприятия, производящие воднодисперсионные лакокрасочные материалы, диоксид титана перевозят в цистернах в виде 65—70 %-ной водной пасты. Операция сушки в технологическом процессе получения TiO2 таким образом исключается.
Недостатком сернокислотного способа является большой расход серной кислоты — 2,1 т на 1 т диоксида титана. Вся серная кислота превращается в отходы: кислые шламы, железный купорос, разбавленную и загрязненную «гидролизную» кислоту и очень разбавленные кислые воды от промывки железного купороса, ГДТ и газовых выбросов.
Железный купорос, получаемый в количестве 3,2—3,6 т на 1 т TiO2, используется в производстве желтых и красных железо-оксидных пигментов и как коагулянт при очистке водопроводной воды. Избыток купороса прокаливают с известью и получают «окатыши» — сырье для доменной выплавки чугуна. Выделяющиеся газы SO2 и SO3 снова превращают в серную кислоту.
Разбавленную 15—20 %-ную гидролизную кислоту концентрировать весьма трудно, так как имеющиеся в ней соли Al, Mg, Fe и другие образуют гелеобразные шламы. Гидролизную кислоту используют для производства удобрения — суперфосфата.
Таким образом, производство диоксида титана сернокислотным способом представляет собой сложный комплекс производств серной кислоты, суперфосфата, железооксидных пигментов и металлургического сырья, а иногда и выплавки чугуна, и все же большое количество шлама и сильно разбавленных кислых промывных вод остается неиспользованным.
Хлоридный способ. Получение пигмента по этому способу основано на хлорировании брикетов из высококонцентрированного титансодержащего сырья с восстановителем коксом в реакторе непрерывного действия при 800 0C:

Одновременно хлорируются и примеси Fe(II и III), Al, Si. Тетрахлорид титана TiCI4 представляет собой жидкость с температурой кипения 1350C и температурой замерзания - 230C. Трихлорид железа — твердое вещество с температурой плавления 282 0C и температурой кипения 3150C. Дихлорид железа FeCl2 — также твердое вещество, возгоняется при 672 0C. Большая разница в температурах кипения хлоридов титана и железа позволяет двухкратной ректификацией разделять продукты хлорирования с получением TiCl4 высокой степени чистоты и отходов SiCl4, FeCl3. Поэтому для хлоридного способа приемлемо сырье только с очень высоким содержанием TiO2(не менее 85 %). На воздухе TiCl4 сильно дымит, гидролизуясь в Ti(OH)4, поэтому вся аппаратура должна быть герметичной и стойкой к действию хлора.
Чистый TiCl4 перерабатывается в TiO2 по одному из двух следующих методов.
1. Окисление
TiCl4воздухом, (разбавленным азотом для снижения температуры):

Реакция проводится в специальной горелке. Хлор, разбавленный азотом, подвергается регенерации и возвращается в процесс хлорирования. Прогрессивным способом является сжигание TiCl4 в плазмотроне, где кислород воздуха предварительно ионизируют нагреванием до 2000 0C с помощью пусковой вольтовой дуги и постоянного высокочастотного электрообогрева. Полученные частицы TiO2 подвергают резкому охлаждению — «закалке» во избежание их роста, агрегации и спекания.
2. Гидролизперегретым до 4000C водяным паром по реакции:

Образующийся в этом процессе анатаз быстро переходит в рутил. Парофазный гидролиз мало применяется, так как необходимо регенерировать хлор из HCl, что требует больших затрат.
Полученный обоими способами высокодисперсный диоксид титана отделяется от реакционных газов в электрофильтрах. Для освобождения от адсорбированных Сl2 или HCl проводится дехлорирование продувкой перегретым паром. Вся аппаратура хлоридного способа производства TiO2 изготовляется из чистого. металлического титана, поэтому продукт не загрязняется и отличается высокой белизной и хорошей разбеливающей способностью. В процессе окисления в зону реакции могут быть введены модификаторы — алюминий и кремний.
Хлоридный процесс производства TiCl4 характеризуется применением особо высокогерметичного оборудования и высокой культурой производства. Это необходимо, чтобы не допускать загрязнения окружающей среды хлором и другими отходами (FeCl2 и FeCl3).
В мировой практике хлоридным способом вырабатывается менее 30% TiO2 но этот способ перспективен, поскольку связан также с получением из TiCl4 чистого металлического титана.